Electric Power Systems
- HOME
- Electric Power Systems
- Transformers
- Utility Transformers
Utility Transformers
Kitashiba manufactures utility transformers by combining its cutting-edge technologies for basic design, production design using 3D CAD systems, and stringent quality assurance. Our utility transformers satisfy various stringent requirements of power plants and substations, including increasingly higher voltage and capacity to meet the growing electricity demands, as well as small size, low noise, and simplified maintenance. Kitashiba’s utility transformers are widely used at various locations for power generation, transmission, transformation, and distribution.
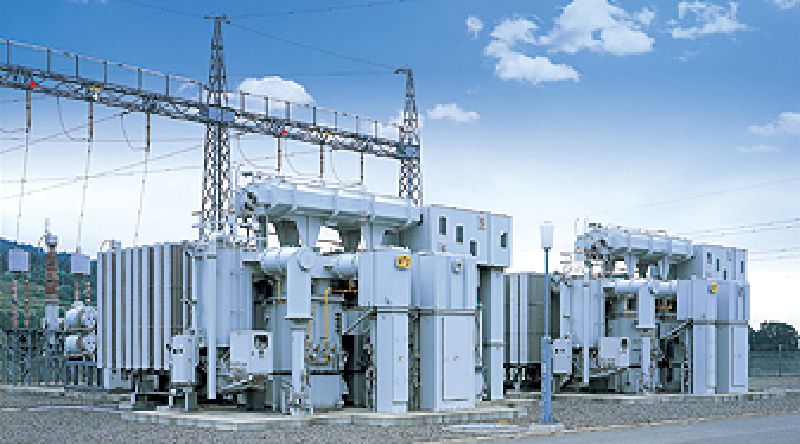
Decades of Experience and Trust
1. High reliability
The reliability of Kitashiba’s utility transformers is supported by a combination of new and well proven technologies accumulated over many years, a sound design with sufficient margins, a controlled work environment, and adequate equipment, as well as stringent work management, quality control, and testing.
2. Low power loss and noise
The coils of Kitashiba’s utility transformers use a frame-type iron core made of grain-oriented silicon steel plates with excellent characteristics, which are stacked in either a staggered pattern at an angle of 45° or a step-lap pattern to provide a smooth magnetic flux flow in the core and thereby achieve low power loss and noise. Kitashiba’s 30-MVA and 10MVA transformers exhibit noise figures of only 45dB(A) and 40dB(A) respectively without a sound-proof tank.
Depending on the magnitude of the electric current, coil windings are manufactured using a paper-wrapped flat conductor, paper-wrapped composite conductor, or a paper-wrapped transition conductor made of high-purity electrolytic copper. Kitashiba employs computers to calculate the eddy current caused by leakage flux crossing the winding to determine the winding size and thereby achieve low power loss.
Analysis of a flux distribution is very useful in understanding the stray loss phenomenon. Windings are tested to ensure that both clamps and the tank are free from local heating.
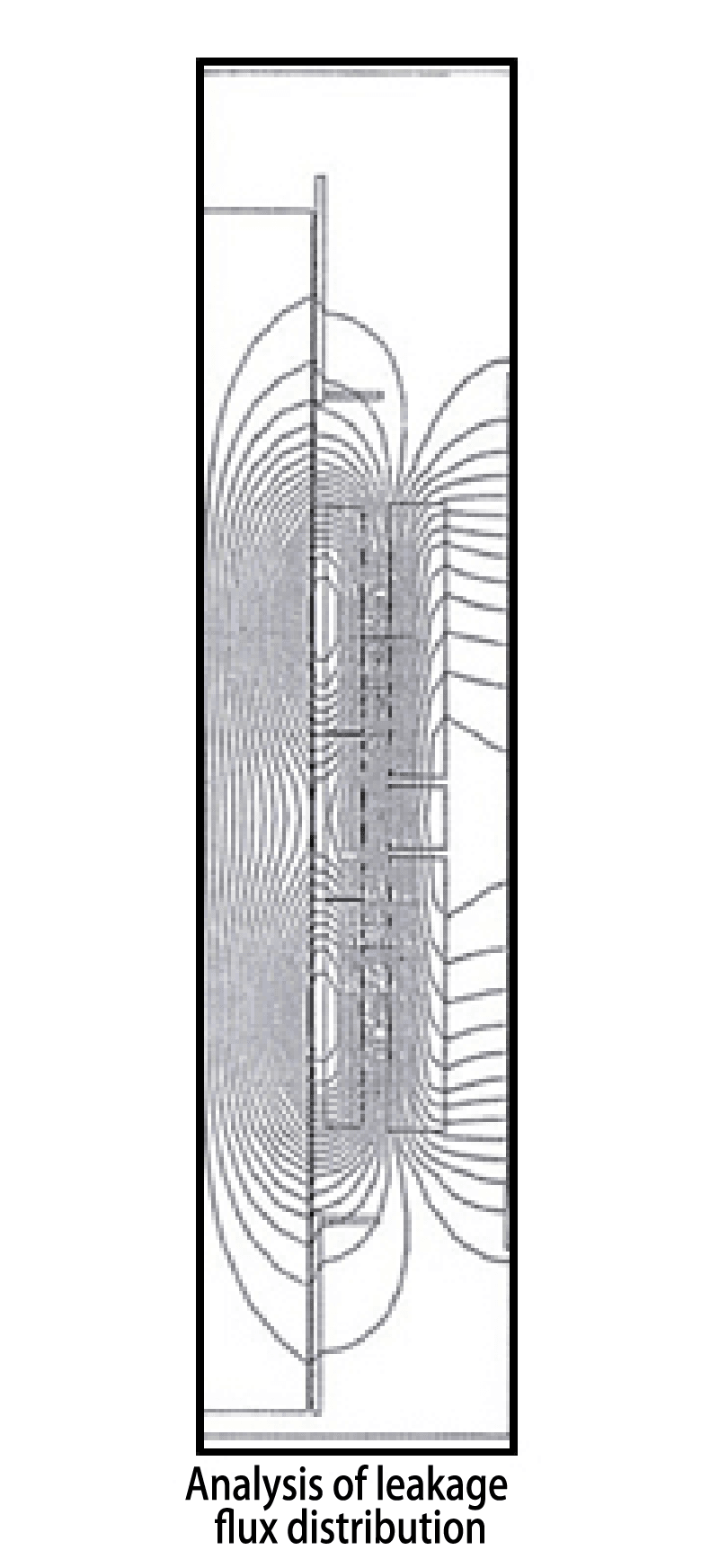
3. Outstanding winding technology
Appropriate windings are used according to specifications. High-voltage windings are formed as high-cell-cap disk windings, multi-layer cylindrical windings, or continuous disk windings that exhibit uniform voltage potential distribution in the event of a lightning impulse, whereas low-voltage windings are manufactured as helical windings, continuous disk windings, or multi-layer cylindrical windings.
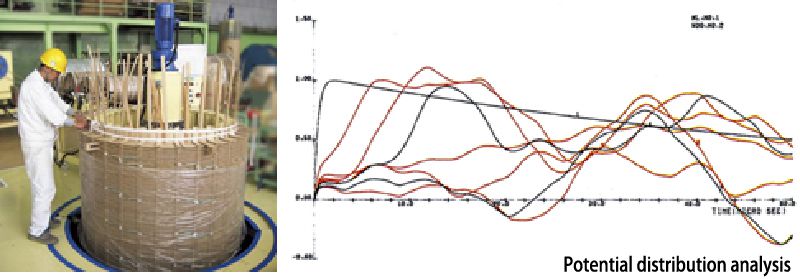
4. Reliable design supported by computer analysis technology
Kitashiba determines design criteria for large transformers, drawing on its extensive experience and technology, and employs computers to build quality into products.
5. Efficient cooling
Oil flows in windings and large iron cores are controlled to improve cooling efficiency (Image 1).
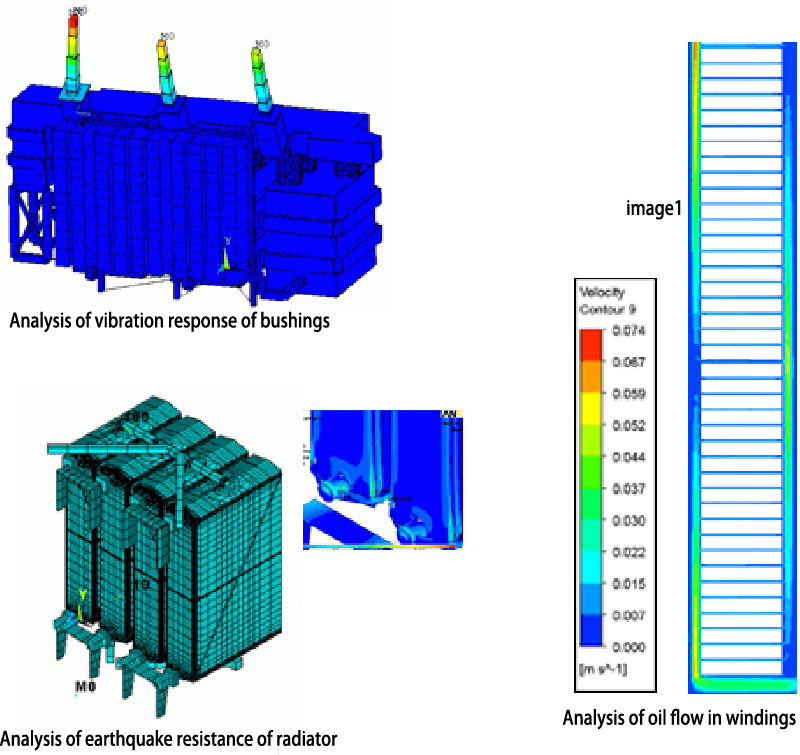
6. Advanced insulation drying process
High-density pressed boards manufactured in a contamination-controlled zone are used to provide electrical insulation and cooling oil channels in the winding assembly. During and after the assembly of the coil and core, state-of-the-art vapor-phase drying (VPD) equipment and optimal drying technology are utilized to minimize the moisture content in the insulation. This is to minimize the contraction of insulators due to aging to prevent the windings from loosening over many years of operation.
7. High short-circuit ruggedness
Kitashiba employs computers to accurately calculate the electromagnetic mechanical force applied to the windings due to the magnetizing inrush current that is produced by an abrupt short-circuit on the secondary side of a transformer and power-up. Based on this result, a conductor and a support structure are selected to ensure sufficient mechanical strength.
8. Easy installation
Transformers with a capacity of 20MVA or less can be transported while fully assembled. Transformers with a larger capacity are disassembled before they are transported, but the coil and core of the transformer are shipped from the factory without being disassembled. Therefore, all that needs to be done at the installation site is to connect bushings to a transformer. This means that Kitashiba’s transformers provide high reliability and can be installed in a short period of time.
9. Reductions in the size and transportation cost of large transformers
In addition to three-phase-integrated transformers, Kitashiba offers two other types of large transformers. One type is disassembled into three single-phase units for the purpose of transportation, whereas the single-tank transformer allows the coil and core for each of the three phases to be transported separately and then placed into a single tank at the installation site.
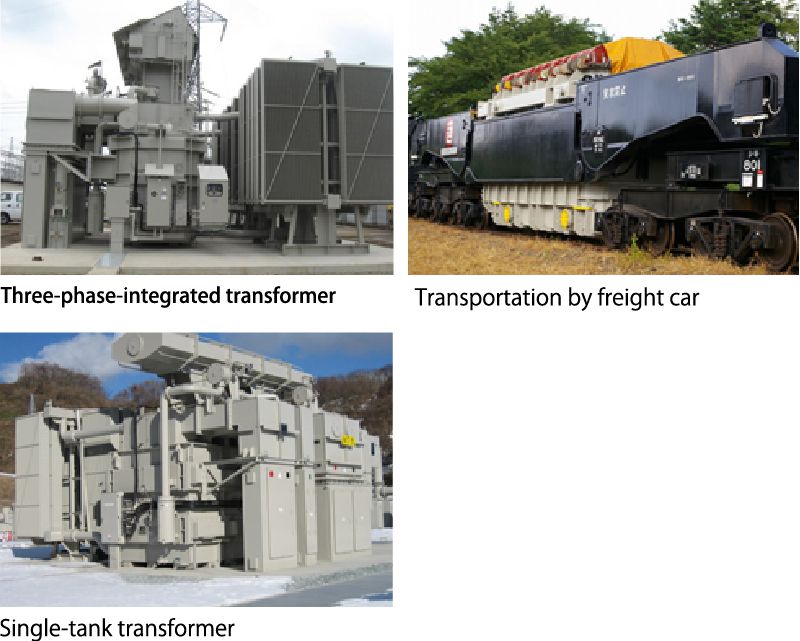
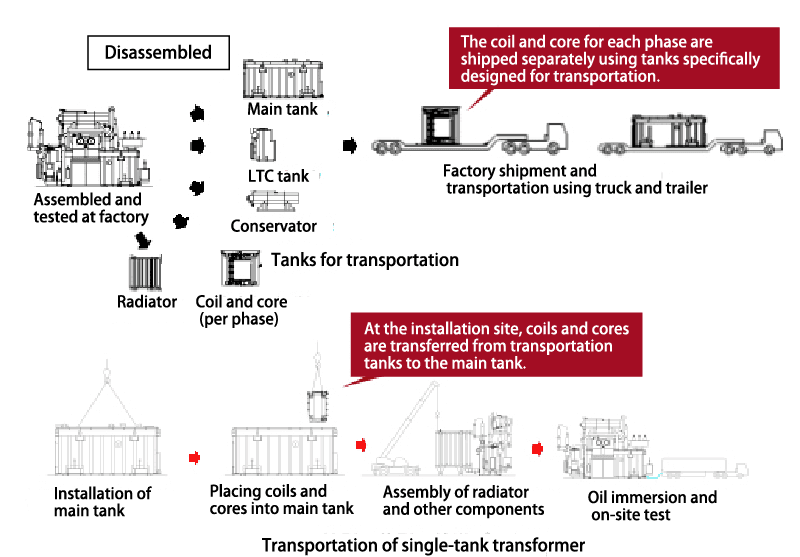
10. Meeting various needs
Kitashiba’s transformers meet customers’ needs in areas such as high reliability, low power loss, low noise, and simplified maintenance due to the use of an on-load tap changer with vacuum interrupters. The transformer that integrates a circuit breaker (CB) and a gas-insulated switchgear (GIS) saves substation space.
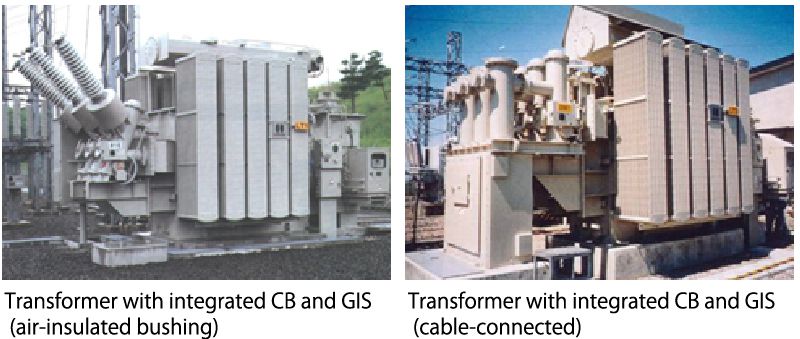