Customer Testimonials
- HOME
- Customer Testimonials
- Industrial Systems
Industrial Systems
Drawing on its extensive experience in manufacturing, Kitashiba offers reliable metal melting systems and facilities that combine its unique induction furnace and semiconductor application technologies. We have reviewed and optimized the design of the entire induction furnace system to develop the Elesave furnace series, which features low environmental load and power consumption.
We have also developed an automatic foundry operation & energy management system (FOMS) incorporating our latest control technology. The FOMS allows you to improve and optimize energy efficiency with the minimum facilities and helps automate the metal melting process and improve the working conditions.
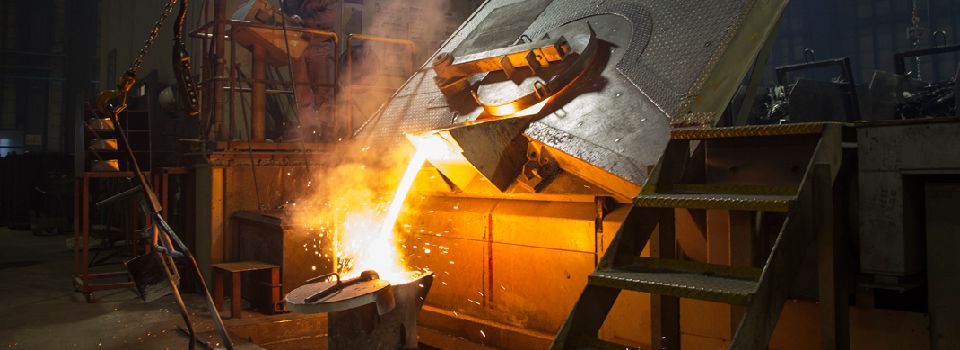
Compact and highly efficient facilities for the new foundry
Aizu Kojyo Co., Ltd., which had been a subsidiary of Naigai-Malleableiron Co., Ltd. in Chiba Prefecture, became independent from Naigai-Malleableiron in 1977. The horizontal controlled pouring process developed by Aizu more than 30 years ago still remains one-of-a-kind technology in Japan. In the summer of 2013, Aizu constructed a new foundry to further improve productivity and help revitalize Fukushima. Based on trust and partnership, Kitashiba was requested to resolve issues so as to realize compact, adaptable, and highly efficient facilities.
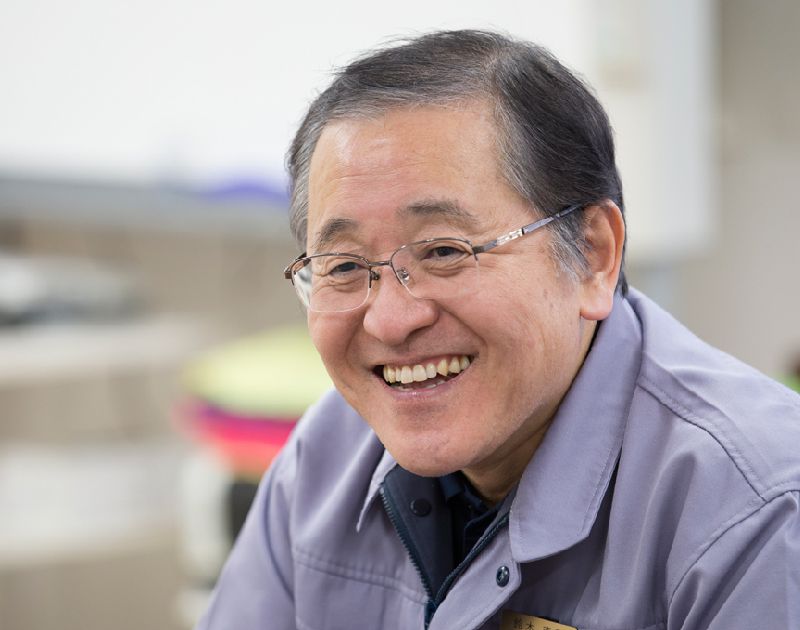
Mr. Naoki Suzuki, President of Aizu Kojyo Co., Ltd.
Manufacturing Precision Castings Using World’s Only Technology
Manufacturing Precision Castings Using World’s Only Technology The horizontal controlled pouring process of Aizu is one-of-a-kind, not only in Japan but also worldwide. This unique process was developed by Aizu as a result of continuous improvements based on the technology developed in Britain. Since then, Aizu has continually endeavored to improve quality and reduce turnaround times, combining the horizontal controlled pouring process and a comprehensive production system, which encompasses the die tooling, casting, heat treatment, and cutting processes.
In Japan, only Aizu performs volume production using the horizontal controlled pouring process. Most of the products from Aizu are automotive components. The high precision and beautiful finish of its castings caught the attention of a sport and outdoor gear manufacturer, and Aizu started working on Dutch ovens, skillets, and other kitchenware in the spring of 2018. Aizu built a new foundry as it was receiving increasing orders. Aizu had been progressively recognized by customers for its efforts. Since its foundry had been operating at almost full capacity since its founding, Aizu had difficulty to keep up with growing demand. “It was around 2010. Following the Great East Japan Earthquake, I was considering building a new foundry, hoping to do what I can do to help rehabilitate Fukushima and to thrive even more,” said President Naoki Suzuki.
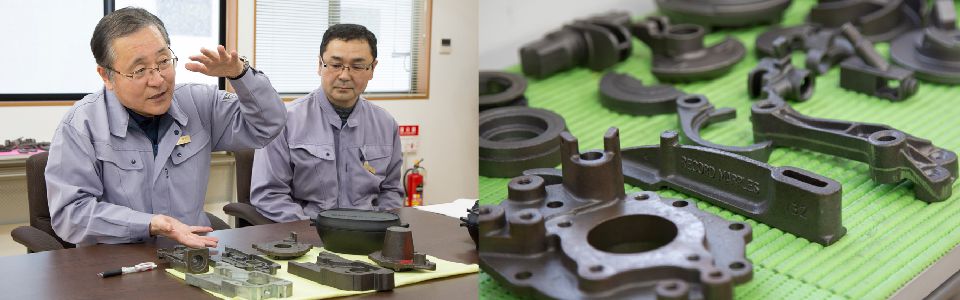
The horizontal controlled pouring process provides a 62% reduction in weight, a 72% reduction in the time required for the cutting process and more beautiful finish than the conventional casting method.
The horizontal controlled pouring process, simply known as the H process, allows repetitious production of castings. Aizu succeeded in efficient, volume production of high-precision ductile iron cast components by using shell molds in the horizontal controlled pouring process. The horizontal controlled pouring process provides close control of casting dimensions, a reduction in casting costs, and small variation in the casting weight, almost eliminating the need for a finishing process to form materials into the final shape. Aizu not only realized a near net shape with a beautiful casting surface but also achieved considerable reductions in the weight and processing time compared with the green sand casting process, reducing total costs.
Encounter with the Elesave High-Efficiency Melting Furnace Series
The Elesave melting furnace fitted the production style of Aizu. “In fact, we have been using large furnaces with a capacity of two tons in order to achieve sufficient production volumes. However, since the melting furnaces had higher throughput than the other processes, they had to stand idle until molds were completed. For example, suppose that you have a production line that requires 24 hours for mold tooling and 10 hours for the melting process. Then, the mold tooling process obviously creates a bottleneck for the subsequent processes. We were unable to synchronize the melting process with other processes.”
If mold tooling takes 24 hours, the melting process should take 24 hours. Then, the overall production proceeds smoothly. As a result of repeated discussions, Aizu decided to introduce two 800-kg melting furnaces. However, there was a concern that using small melting furnaces might decrease efficiency. In retrospect, President Suzuki says, “I considered how much electricity it takes to melt iron. I asked Kitashiba whether it has any plan that would help increase the basic melting unit and reduce the furnace size. Surprisingly, I was told that Kitashiba had just developed a new voltage-type high-efficiency melting furnace called Elesave. It was perfect timing for us.”
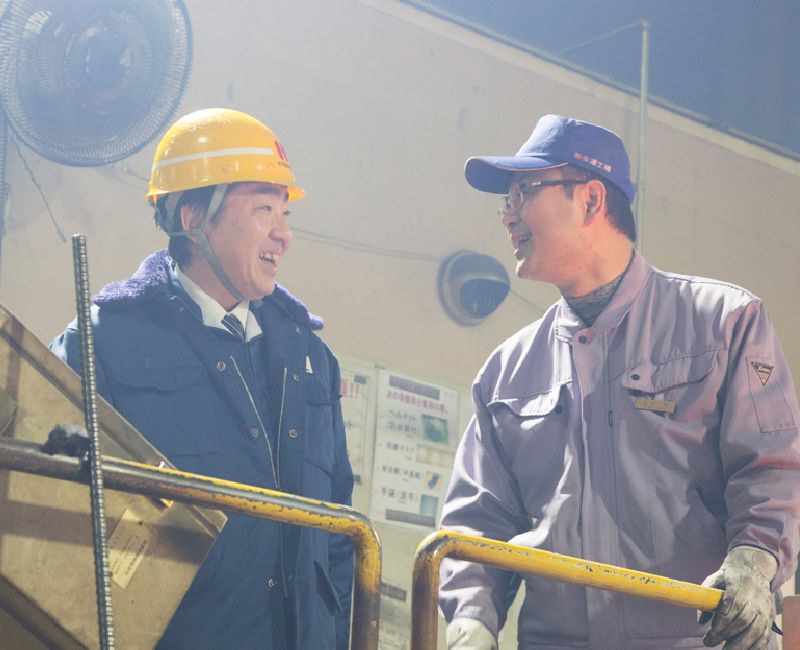
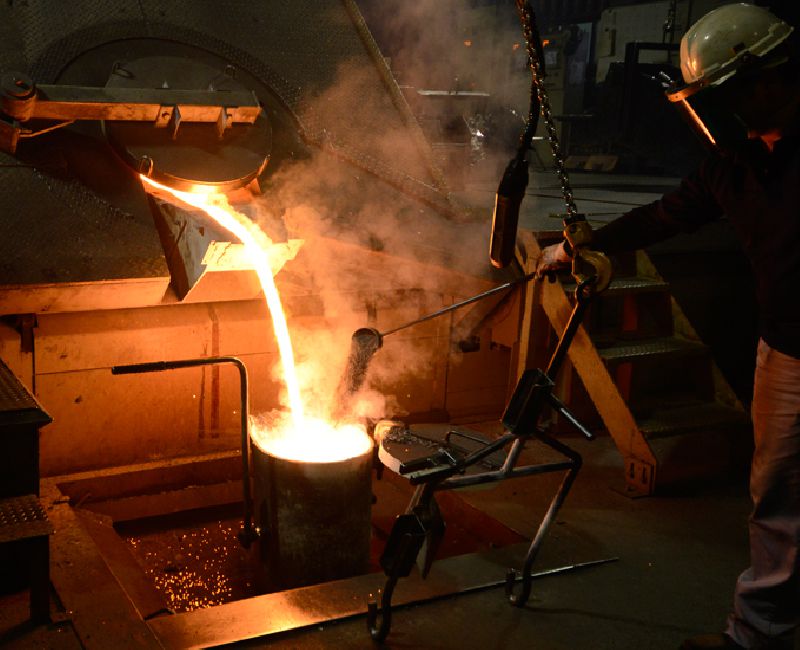
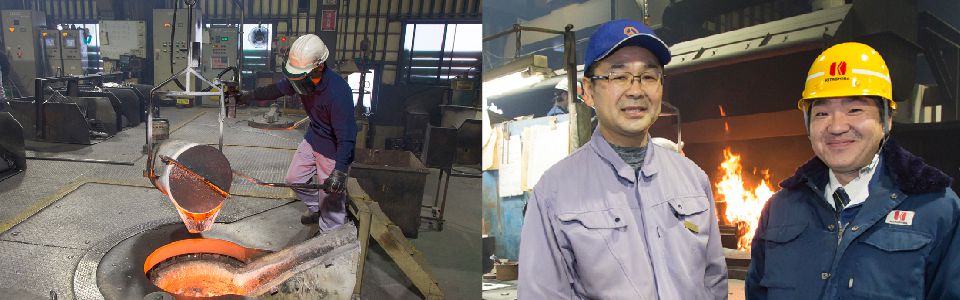
Encounter with the Elesave High-Efficiency Melting Furnace Series
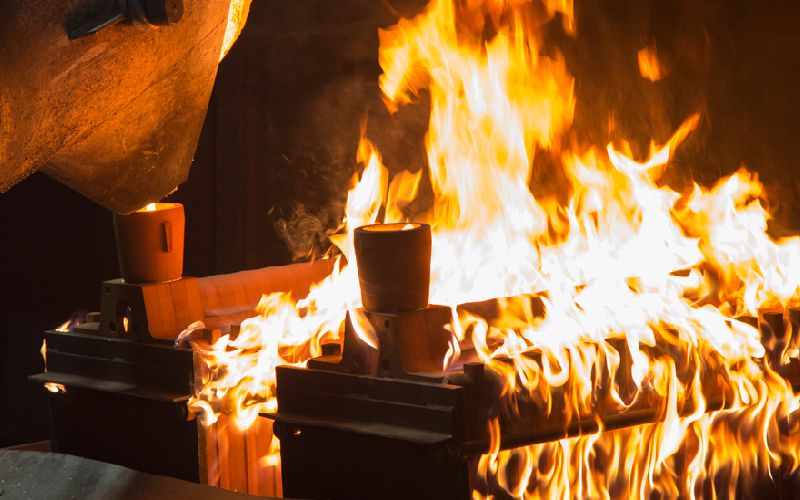
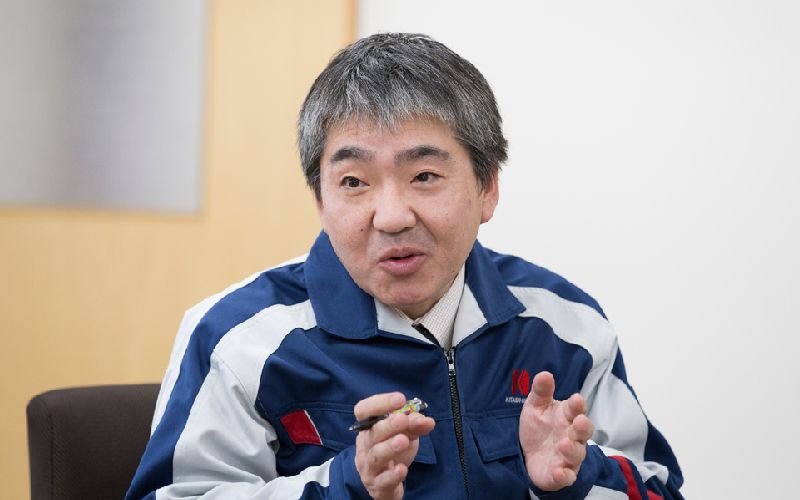
Hiroki Saito, Deputy Manager
Sales Group, Promotion Department, Industrial Systems Division of Kitashiba Electric Co., Ltd.
It was not long since the Elesave furnace series had been developed. President Suzuki told us later that he felt a little bit uncertain because Elesave did not have a proven track record. President Suzuki said that he selected Elesave since he had been using Kitashiba’s melting furnaces for nearly 40 years since Aizu was a subsidiary of Naigai-Malleableiron. “Indeed, it is true that performance and price are important, but good service is even more important. If a melting furnace goes out of order in the evening, a service person of Kitashiba comes to repair it at night so that we can start the melting process next morning. I wonder how many times Kitashiba has offered us a helping hand before.” President Suzuki continued. “Aizu and Kitashiba work in tandem. In a sense, we are in the same boat. I wanted to cooperate and grow with Kitashiba. That is why I placed an order for two melting furnaces with Kitashiba.”
In order to realize compact, adaptable, and highly efficient facilities, Aizu and Kitashiba collaborated to solve the problems of the melting and casting cooling lines. We worked out details of the facilities in close partnership. “Kitashiba’s people came to meet us so often. I jokingly thought they should have time cards to record their clock-in and clock-out times here.”
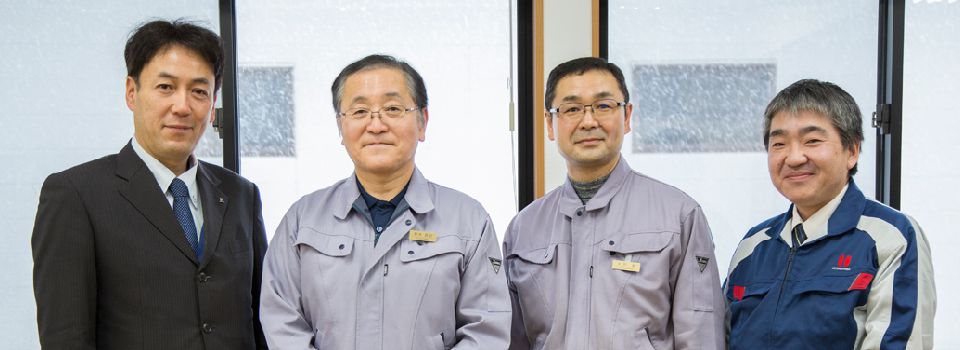
A full two years has passed since the new foundry was completed.
When asked about the degree of attainment of efficiency and energy-saving targets, President Suzuki said, smiling all over, “We have almost attained the targeted results.” “The new melting furnace consumes roughly 10% less power than the old one. It might be difficult to imagine how much it amounts to, but it is a big difference since we pay unusually high electricity bills for the melting process.” Previously, Aizu employed a melting process in which a fragment of two-ton molten iron is left in the furnace before new iron is added. Now, all the molten iron can be discharged from the melting furnace without adversely affecting the throughput. Previously, Aizu had two two-ton furnaces. Therefore, after a single run of the melting process, Aizu had to manufacture four-ton castings. “Now, we have two 800-kg melting furnaces, with a total capacity of 1.6 tons. So, we can draw up flexible production plans according to the amounts and types of castings to be manufactured. We can now adapt to customers’ orders more flexibly.”
When asked about what he expects of Kitashiba in the future, President Suzuki mentioned FOMS, which Kitashiba proposed as a means of further improving efficiency. “In short, we need a system that monitors our electricity use” I want to reduce the overall energy consumption of the foundry by using a system that improves and optimizes energy efficiency with minimum facilities.” In addition, President Suzuki requested a stock of replacement parts so that we can promptly respond in the event of a failure of a melting furnace. Thank you for your suggestion. In order to further enhance our monozukuri capabilities (i.e.., art, science, and craft of making things), we would like to cooperate with Aizu based on respectful partnership. We look forward to continuing to work with Aizu.