Electric Power Systems
- HOME
- Electric Power Systems
- Hydric Turbine Generators
Hydric Turbine Generators
Kitashiba’s high-efficiency, high-reliability, and low-maintenance hydric turbine generators are custom-designed using cutting-edge analysis technology and low-loss materials to suit the geographical conditions of the sites where each customer plans to construct a hydroelectric power plant. Kitashiba also has extensive experience in generator maintenance. Kitashiba can refurbish stators and rotors and replace brushed exciters with brushless exciters according to customers’ requirements.
Vertical-Type Hydric Turbine Generators
Kitashiba manufactures various vertical-type hydric turbine generators with eight or more poles according to the water supply conditions. Kitashiba’s vertical-type hydric turbine generators are available with a wide range of capacities from 1,000kVA to 10,000kVA.
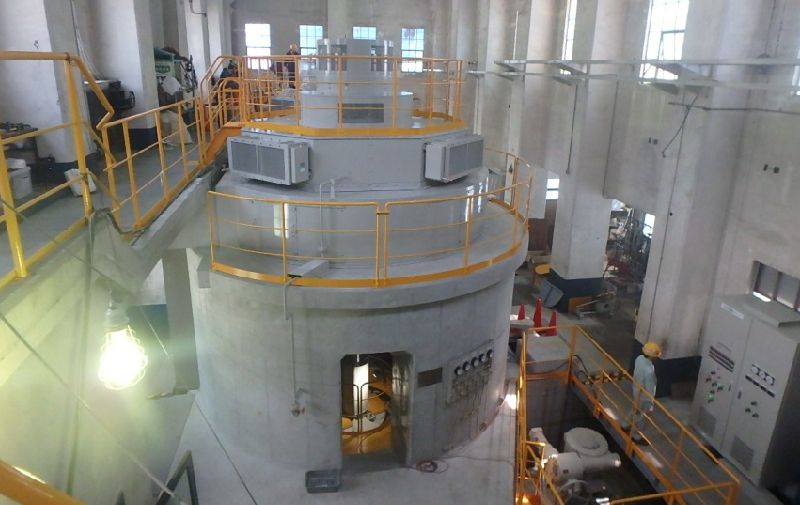
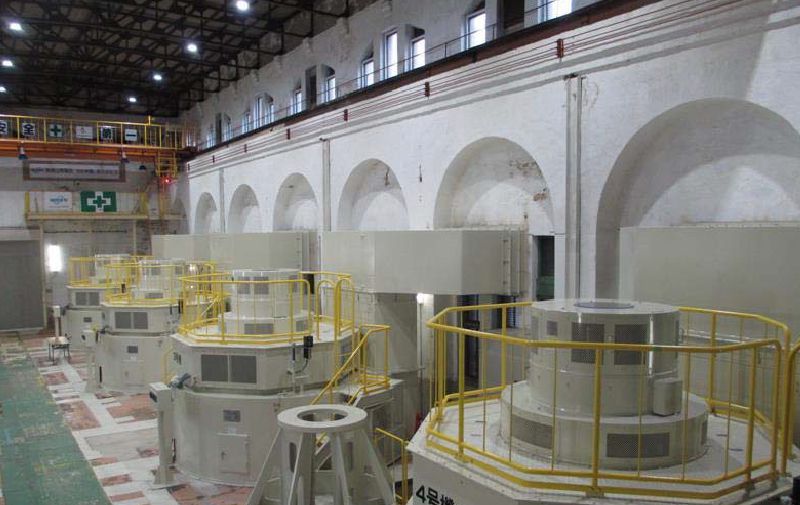
Horizontal-Type Hydric Turbine Generators
Kitashiba manufactures various hydric turbine generators that conform to Francis, Pelton, and other types of turbines. Kitashiba’s horizontal-type hydric turbine generators are available in a wide range of capacities from 200kVA to 10,000kVA.
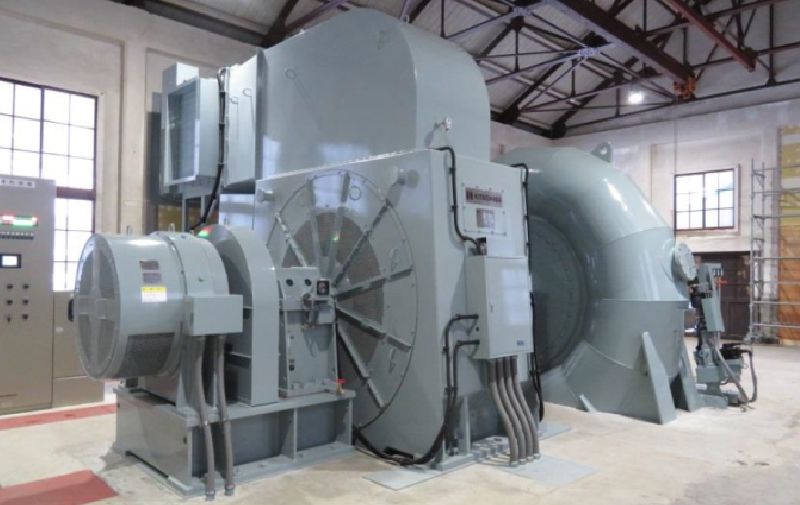
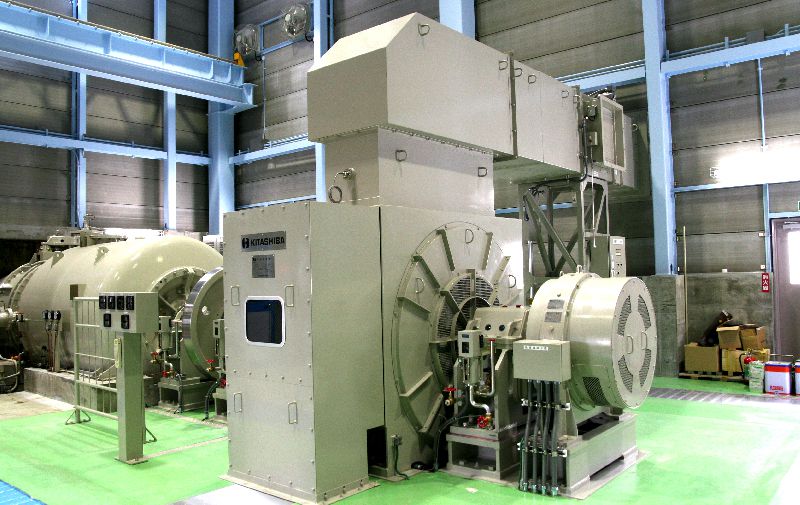
Comprehensive Generator Maintenance Services
Kitashiba offers comprehensive maintenance services, including the replacement of stator coils, stator cores, rotor coils, bearings, and other components of outdated hydric turbine generators, modification for using brushless exciters, and estimation of the remaining life expectancy via insulation diagnosis. By employing state-of-the-art insulation technology, low-loss coil cores, and measures to prevent reduction in coils’ insulation resistance, Kitashiba turns an old hydric turbine generator into a high-reliability, high-efficiency, and low-maintenance generator. Kitashiba is highly trusted by its customers as it has offered these maintenance services for roughly 350 hydric turbine generators since 1970.
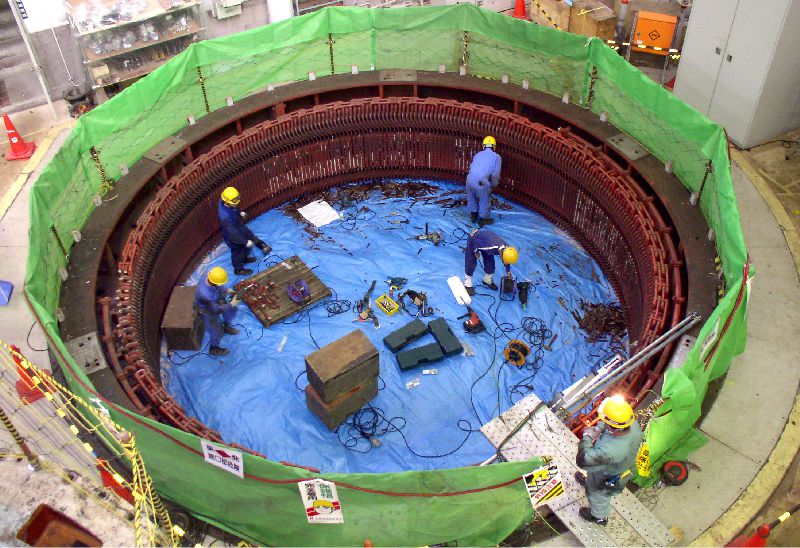
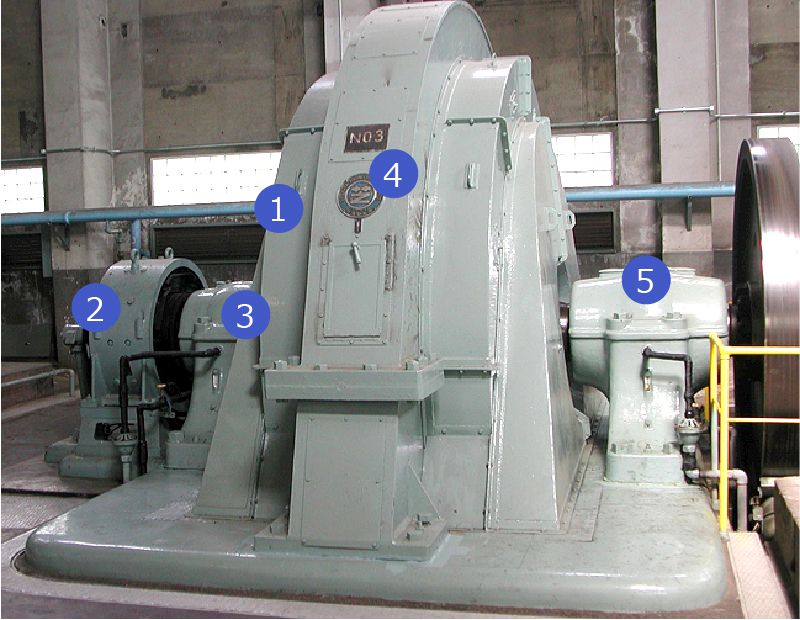
Rotor
- Manufacture of new rotor coils (replacement of rotor coil insulation)
- Prevention of reduction in the insulation resistance of rotor coils
- Manufacture of new rotor magnetic poles
- Nondestructive inspection of the generator shaft
Exciter
- Modification for using a brushless exciter
- Use of a stationary exciter
- Sharpening the outside of commutators
Collector brush
- Manufacture of a new collector
- Manufacture of a new brush holder
- Outer rotation of collector
Stator
- Manufacture of new stator coils
- Manufacture of a new stator core
- Manufacture of a new stator frame
- Inspection or replacement of stator wedges
- Dust collection filter
Bearing
- Manufacture of a new bearing (modification for using a self-cooled bearing with self-contained lubrication)
- Casting of white metals
- Modification for using a resin/metal composite bearing
- Preventive measure for oil leakage
- Nondestructive inspection