お客様の声
Customer's Voice- HOME
- お客様の声
- 産業システム
産業システム
北芝電機では、豊富な製作実績と経験を基に独自の誘導炉技術と半導体応用技術を集結させ、信頼性の高い溶解製品・設備を供給しています。この度、システム全体を設計段階から見直し最適化を図った新開発の「エレセーブファーネスシリーズ」は、環境負荷が少なく電力使用量を抑えることができます。
また、最新の制御技術を駆使した自動制御システム「FOMS(フォムス・Foundry Operation & Energy Management System)」も開発。最小限の設備でエネルギー効率化&最適化を実現するFOMSで溶解作業の自動化、作業環境の改善に寄与しています。
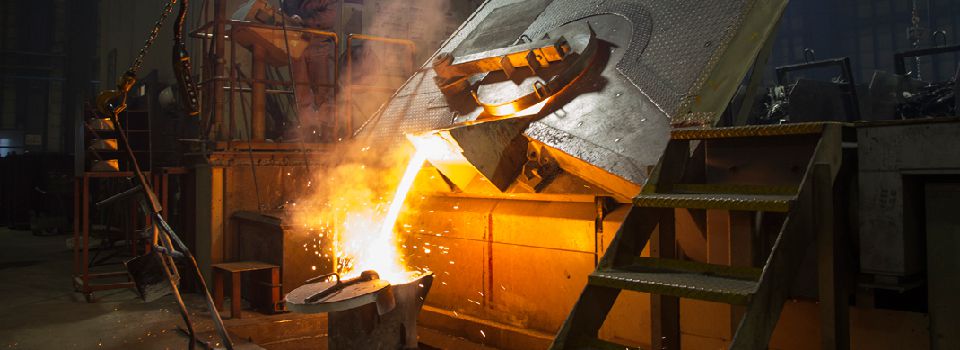
新社屋に期待する「よりコンパクトで高能率な設備」を実現
株式会社会津工場は、内外マリアブル株式会社(千葉県)の子会社を経て昭和52年に独立しました。30年以上前に会津工場が開発した独自の技術「Hプロセス精密鋳造」は、日本で唯一と言われています。平成25年夏、生産性向上と福島の復興を願い新工場立ち上げの際には、信頼とパートナーシップで「よりコンパクトで小回りが利き、なおかつ高能率な設備を」という課題解決に導きました。
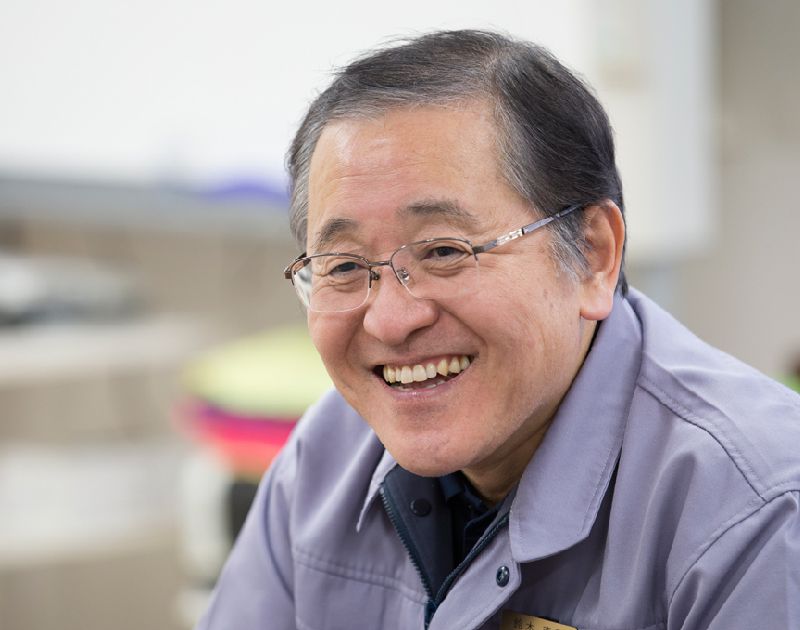
株式会社会津工場
代表取締役社長 鈴木 直記さん
世界唯一の技術で精密鋳造部品を製作する企業
日本国内に留まらず世界唯一ともいわれる(株)会津工場のHプロセス精密鋳造は、英国で開発された技術を導入した後、会津工場でさまざまな改良を重ねながら独自の工法に育てあげた手法です。以来、会津工場は、Hプロセス精密鋳造の技術と、金型―鋳造―熱処理・切削加工の社内一貫生産を両輪に、品質と短納期に挑戦し続けてきました。
ちなみに、この手法で本格的な量産を行っているのは、国内では会津工場のみです。製品のほとんどは自動車部品ですが、高精度でかつ仕上がりの美しさがスポーツ&アウトドア用品のメーカーの目に留まり、同30年春からダッチオーブンやスキレットなどキッチンまわりでも活躍する鋳物製品も手掛けるようになりました。この度の新社屋建設も受注が増えたことがきっかけでした。会津工場の努力が少しずつお客様に認められるようになり、創業当時からの鋳造設備がほぼフル稼働になってきたことから生産設備が追い付かなくなってきたのです。「平成22年頃のことです。翌年の大震災からの復興という願いも込め新しい工場を建てて、またさらに躍進しようと考えました」と鈴木直記社長。
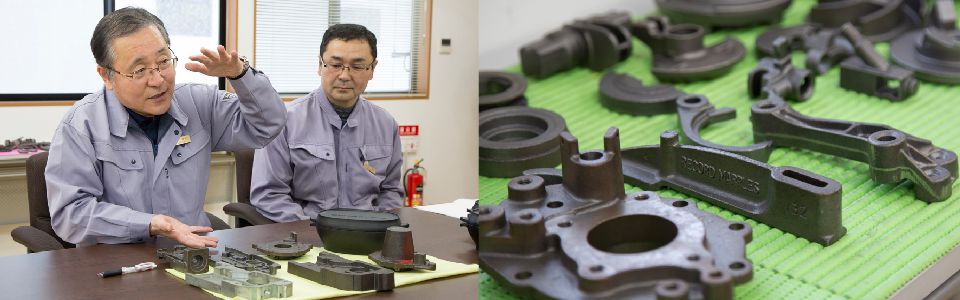
Hプロセス鋳造製品は、従来の鋳物品より重量で62%減、切削加工工数で72%減など、大幅に削減できるほか、仕上がりも美しい。
Hプロセス鋳造法は、横スタック鋳造法とも呼べる技術で、一時に多数個の鋳物を鋳造する手法のこと。会津工場では、Hプロセス鋳造法にシェルモールドを採用することで高精度のダクタイル鋳鉄鋳物部品を効率よく量産化することに成功した。同法で製造される鋳造品は、寸法精度が高く、加工代、重量バラツキがともに小さく、材料を最終形状にするための仕上げがほぼ不要。鋳肌の美しいニヤネットシェイプを実現しただけでなく、生砂鋳造法に比べ鋳造品の重量、加工工数ともに大幅に削減できることからトータルコストも削減した。
高効率溶解炉『エレセーブファーネスシリーズ』との出合い
会津工場の生産スタイルに合う溶解設備でした。「実は、ある程度生産量を確保するために、弊社ではずっと2トンという大きな溶解炉を使っていました。ところが溶解炉だけが勝っているので、鋳型ができるまで溶解炉を待たせなければなりませんでした。例えばですが…鋳型の製作時間が24時間で、溶解工程10時間で生産するラインを想像してみてください。当然、次の工程も大変になっていきます。生産における他の工程との同期化ができないことがこれまでの悩みでした」。
鋳型を作る工程が24時間であれば、溶解も24時間にした方が時間あたりの流れが非常にスムーズになります。検討を重ね出した答えが、800キロの溶解炉を2基導入するというものでした。ただし、溶解炉の小型化は、効率が悪くなるかもしれないという心配も内包していました。当時を鈴木社長は、こう振り返ります。「鉄を溶かすのにどれくらいの電気が必要なのかなども考えました。原単位もよくなり、小型化も叶えるプランはないものかと思って北芝電機に相談すると、なんと電圧型の高効率溶解炉『エレセーブファーネスシリーズ』を新しく開発したばかりだというのです。すごいタイミングで非常によい提案を受けることができました」。
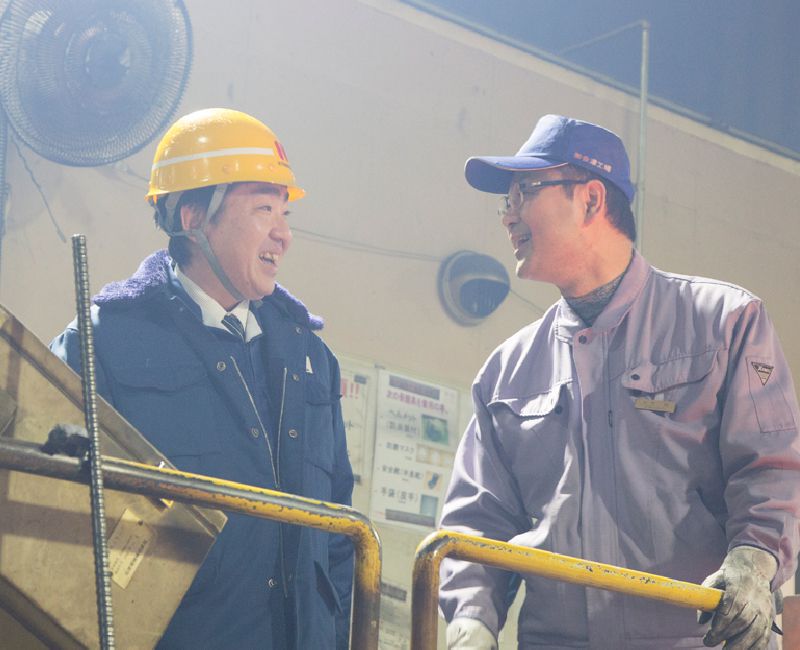
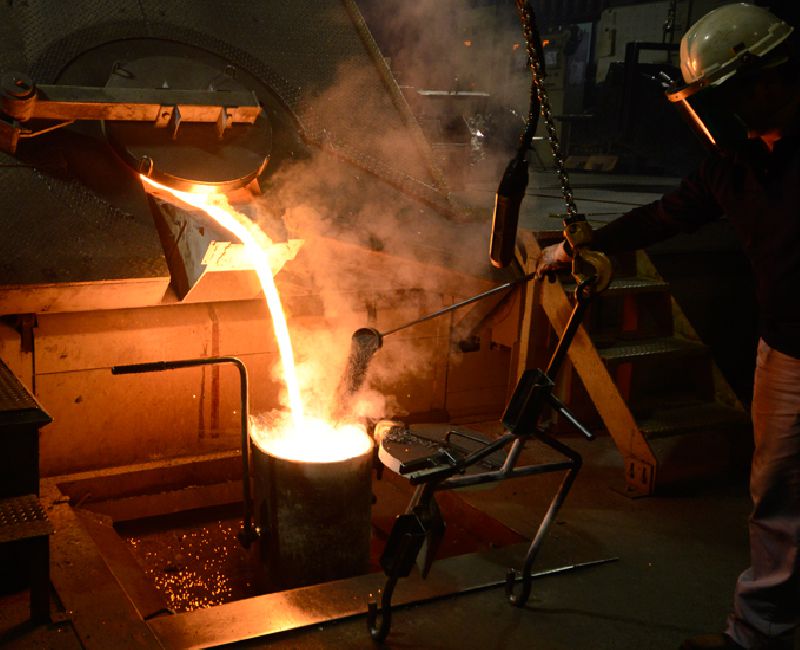
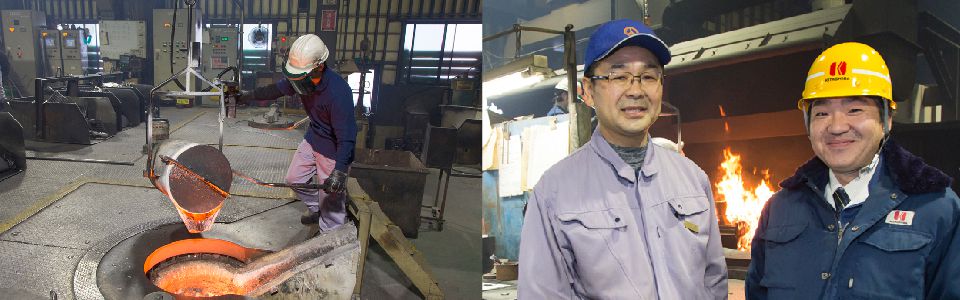
性能、コスト以上に重要なカギを握るサービス面
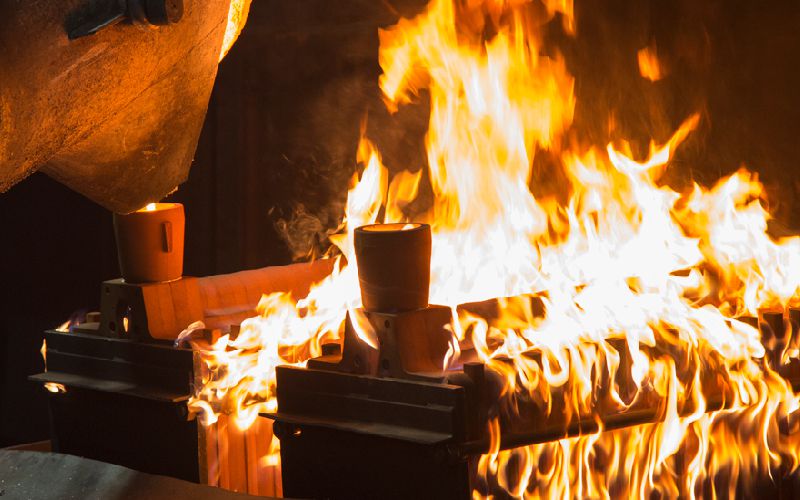
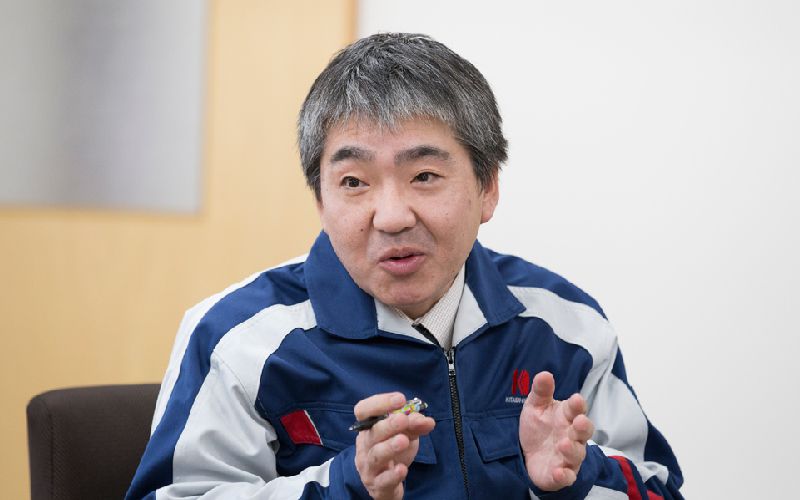
産業システム営業グループ
課長代理 齊藤 弘樹
ところで『エレセーブファーネスシリーズ』は、開発されて日が浅い溶解炉です。実績と言う部分では少し迷った時もあったそうです。しかし、鈴木社長は内外マリアブル株式会社の子会社だった頃から、約40年にわたり北芝電機の溶解炉を使っていたことが、この度の発注につながったとも話しました。「確かに製品の性能、コストも重要ですが、それ以上に大切なのがサービス面です。夕方溶解炉の調子が悪くなった時など、北芝さんは夜でも駆けつけて翌朝一番の溶解に間に合うように修理してくださいます。これまでに何度助けていただいたことか」。鈴木社長は続けます。「やはり鋳物関係で一緒に仕事をしているわけですから弊社と北芝さんはある意味、運命共同体とも言えます。互いに協力し合い、共に実績を積みながら成長していければいいと思いまして2基注文しました」。
よりコンパクトで小回りが利き、なおかつ高能率な設備を実現するため北芝電機は、溶解ライン、鋳造冷却ラインなどの課題解決にも加わり、設備の一つ一つを熱いパートナーシップで詰めていきました。「北芝さんには、弊社にタイムカードを置いてもいいぐらい通っていただきました(笑)」。
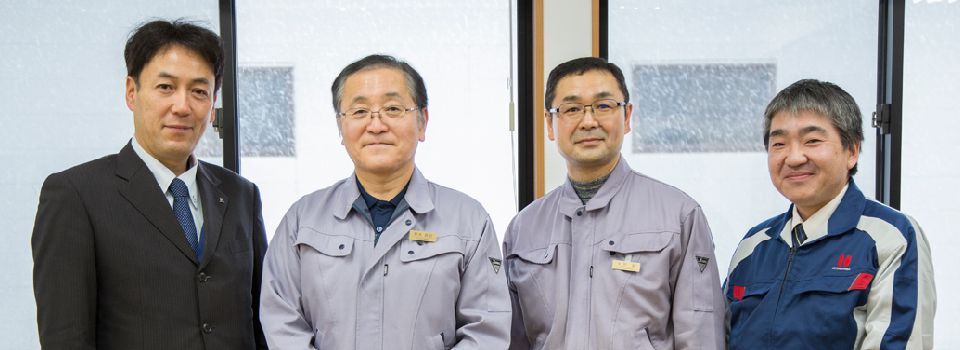
新社屋の満足度。高効率化も省エネ化もほぼ狙い通り
新社屋完成から丸2年が過ぎました。高効率化、省エネ化などの達成度を伺うと鈴木社長は満面の笑みで「実績でいうとほぼ狙い通りです」と答えました。「旧設備より従来比で約10%は改善されていますね。10%というとイメージしにくいかもしれませんが、弊社の溶解電気料は桁が違いますので(笑)」。以前は、残とう溶解といって溶解炉の中で溶けている2トンの鉄を少しだけ残して、新たに鉄を投入するという方法を取っていました。今は鉄を全部出してもスピードを保ったまま作業ができます。また、以前は2トンの炉が2基ありましたので1回溶かすと、必ず4トンの生産をしなければなりませんでした。「今は、800キロが2基ですので、2つ合わせても1トン600キロ。生産の量と種類に応じた小回りの利く生産計画を立てられるようになりました。お客さまの受注に、より柔軟に対応できるようになりました」。
これから期待することとして、北芝電機が高効率を実現させるための方法としてご提案させていただいたFOMS(フォムス)にも触れられました。「要するに電気の使用量を監視できるシステムです。最小限の設備でエネルギー効率化と最適化を実現するというシステムをうまく利用しながら、工場全体の省エネにつなげていきたいと思っています」。さらに万が一、溶解炉が壊れたときの迅速な手当として交換部品のストック体制の講習会についてもご提案いただきました。ありがとうございます。これからもリスペクトしながらパートナーシップで、よりよりよいものづくりのためさらに精進していきたいと思います。引き続きどうぞよろしくお願いします。